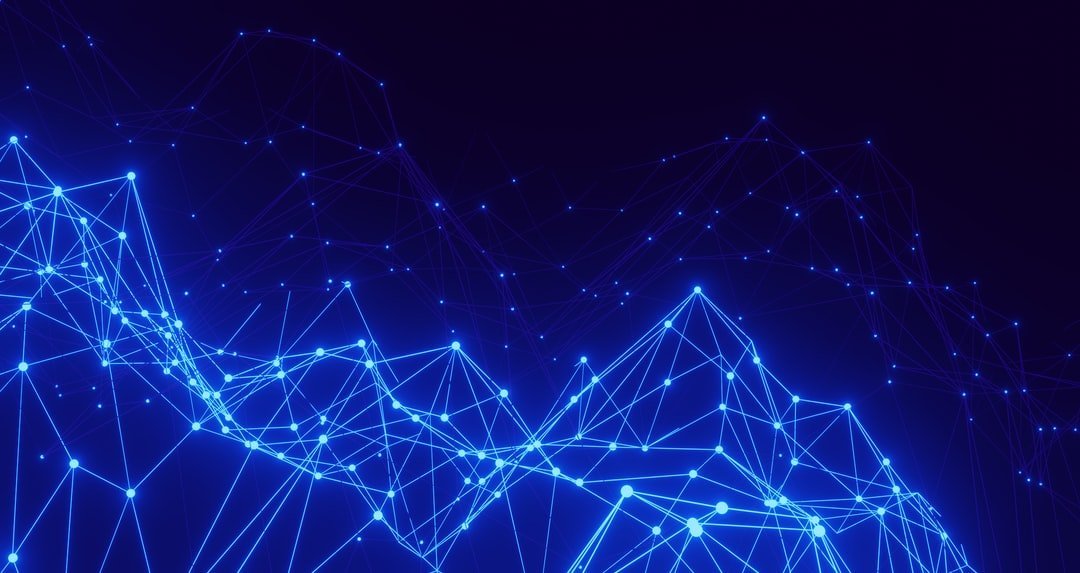
Maximo Case Studies
UTILITIES
Cheniere Energy, Inc.
SEIZING NEW OPPORTUNITIES AND SUPPORTING BUSINESS TRANSFORMATION WITH IBM MAXIMO ASSET MANAGEMENT
Cheniere partnered with Cohesive Solutions to deploy an IBM® Maximo® Asset Management solution that is transforming the maintenance of complex assets at the upgraded Sabine Pass facility.
BUSINESS CHALLENGE
To take advantage of the US shale boom, Cheniere Energy decided to transform its Sabine Pass terminal from importing and re-gasifying LNG to liquefying and exporting it—a much more complex process.
TRANSFORMATION
Cheniere partnered with Cohesive Solutions to deploy an IBM Maximo Asset Management solution that is transforming the maintenance of complex assets at the upgraded Sabine Pass facility.
RESULTS
Boosts
efficiency by aligning maintenance work with the demands of the assets
Maximizes
uptime, improves safety, and facilitates compliance
Reduces
costs with smarter maintenance and inventory management
BUSINESS CHALLENGE STORY
Adapting to a new business model
In just a few short years, the US energy industry has undergone an incredible transformation. With the shale revolution sparking unprecedented production of oil and natural gas, the US has gone from a country that was once importing the majority of its supply to the largest producer of natural gas in the world.
Cheniere Energy’s story offers a prime example of just how dramatically the shale boom has reshaped the natural gas market. The company was building import terminals at Sabine Pass to import and re-gasify liquefied natural gas (LNG) to meet domestic needs. When the shale boom hit, Cheniere made a bold move—it began building liquefaction capabilities at the Sabine Pass terminal, converting it into the world’s first bi-directional LNG facility, capable of liquefying and exporting natural gas as well as importing and re-gasifying foreign-sourced LNG.
The decision to add liquefaction capabilities to the Sabine Pass terminal changed the entire scope of the business. The company has evolved from a straightforward LNG importer to the owner of the first liquefaction facility built in the lower 48 states of the US in the last 40 years.
As a result, the company is primed to reconnect US natural gas producers to customers and markets around the world. To help ensure success, Cheniere is taking all of the necessary steps to ensure smooth operations of its liquefaction operations.
Ahmad Mousselli, Director, Operations Applications, elaborates: “Liquefying natural gas is a very complex process, involving huge production lines known as ‘trains’, which comprise many thousands of high-tech components that need to be operational 24/7. It’s critical for us to keep all of these assets in good working order, as downtime could interrupt production and impact profitability.
“As the scope of our operations expanded, it became clear that we needed to make some significant changes to inventory and work management processes in order to keep our facilities running efficiently, and maintain the strong focus on safety and environmental responsibility that is the cornerstone of Cheniere’s business.”
Ivan de Lorenzo, Outage Planning Manager, adds: “We knew a key factor to ensure the success of our transformation was to develop solid and detailed business processes, so we spent several months mapping all relevant maintenance, procurement and financial processes. This was a great effort, but it paid off by ensuring a much smoother transition to our new business model.”
TRANSFORMATION STORY
Upgraded asset management
Cheniere initially planned to reconfigure its existing enterprise asset management [EAM] system, but after extensive evaluation, the company realized that the system simply could not offer the level of flexibility and functionality that it needed. Instead, Cheniere decided to adopt a new EAM platform that could support its re-engineered business processes from end to end. The solution the company selected was IBM Maximo for Oil and Gas, a solution from the IBM Watson IoT (Internet of Things) portfolio.
To help guide a smooth implementation, Cheniere joined forces with IBM Premier Business Partner Cohesive Solutions. Ahmad Mousselli notes: “Cohesive impressed us with their deep business and functional knowledge. They had proven experience of implementing Maximo solutions for other oil and gas companies, and we were confident that they could help us deliver a successful project.”
Cheniere established a tight implementation schedule, completing the project in just one year—a feat made even more impressive by the fact that the company also re-implemented its Oracle E-Business Suite Financials applications during the same timeframe.
Russ Anderton, Vice President at Cohesive, remarks: “What Cheniere has accomplished is truly remarkable: I personally have never seen a company pull off parallel implementation projects of this magnitude in such a short timeframe. Implementing EAM and ERP systems at the same time was incredibly ambitious. The fact that Cheniere was successful is a testament to the company’s investment in business process engineering, project management and change management, rather than just focusing on the technical aspects of the project.”
Ivan de Lorenzo adds: “On the integration side, there are multiple business scenarios and configuration options to consider. With the short timeframe available, we needed a fast response time to be able to cope with unknowns and last minute changes. This was possible thanks to Maximo’s flexibility and Cohesive’s strong expertise.”
Today, Cheniere has established consistent, optimized business processes across the entire asset lifecycle, from inventory control and work management to monitoring and maintenance—all supported by IBM Maximo for Oil and Gas. The Maximo solution has various integrations with the company’s Oracle Financials applications, which enable seamless end-to-end management of processes that involve both financial and operational dataflows.
For example, when a work order is created, a Maximo workflow routes it through review, financial approval, planning and scheduling to completion. If the work order requires a purchase to be made, then Maximo creates the purchase requisition and immediately routes it to Oracle Financials for approval. Oracle then handles the purchase order and invoice management processes.
Cheniere is also making use of Maximo’s reporting capabilities to give teams better insight into assets, work schedules and operational performance.
Ivan de Lorenzo explains: “We have defined more than 50 custom reports for our Maximo users, especially maintenance personnel. The reports include daily and weekly work schedules, which they are finding very useful. Reporting in Maximo is very flexible and easy to get to grips with—some of our users are already generating their own reports. We’re also in the process of setting up key performance indicators, using a solution from Cohesive that will help us view our business performance easily, both at the strategic and tactical levels.”
RESULTS STORY
Driving operational excellence
With improved business processes and insight into company-wide activity, Cheniere is unlocking new efficiencies and achieving higher operational quality—particularly around maintenance planning and scheduling.
Ivan de Lorenzo notes: “We have better information on assets and maintenance activity, and more sophisticated tools and mechanisms for managing it all. The result is greater operational control and accountability, especially when it comes to planning and scheduling. For example, the service request and work order workflows have allowed us to automatically route each job to a specific team or individual, improving response time and accountability.”
Ahmad Mousselli adds: “IBM Maximo is a great solution—it definitely allows us to work more efficiently. We can better analyze resource availability and assign the right people for the job faster, leading to less re-work and improved response times. This ultimately means that we can meet business requirements more quickly and efficiently, minimizing costly downtime and keeping our facilities running safely.”
By building up a rich store of data on how its assets perform over time, Cheniere will ultimately be able to enable predictive maintenance, optimize maintenance and repair work to prolong the life of assets, avoid unexpected downtime, and reduce costs.
Ivan de Lorenzo says: “We are currently performing live monitoring of the runtime of our assets, using an OSIsoft PI Historian solution which Cohesive integrated to Maximo. Once we have accumulated a couple of years of historical data and established some benchmarks and other metrics for maintenance intervals, we expect to optimize maintenance planning so we can co-ordinate resources more effectively and maximize equipment uptime.”
Ahmad Mousselli concludes: “The last few years have been a time of great transformation for Cheniere. With IBM Maximo software supporting our new operational processes, we have the strong foundation we need to continue developing a leading LNG platform—one that has the potential to change the dynamics of natural gas markets both in the US and worldwide.”
Cheniere Energy, Inc.
Cheniere Energy, Inc., a Houston-based energy company primarily engaged in liquefied natural gas (LNG)-related businesses, owns and operates the Sabine Pass LNG terminal and Creole Trail Pipeline in Louisiana. Through its subsidiary, Cheniere Energy Partners, L.P., Cheniere is developing liquefaction projects at the Sabine Pass LNG terminal. Cheniere is also developing an LNG liquefaction plant near Corpus Christi, Texas and exploring a limited number of opportunities directly related to its existing LNG business.
SOLUTION COMPONENTS
C&P/IP: Industry 4.0 Platform
Enterprise Asset Management
Maximo Portfolio
Oracle EBS Financial Management